罗泷,徐立军
(钢铁研究总院冶金工艺研究所,北京 100081)
摘 要:电渣炉通过控制电流摆动范围等效地保持电极端部侵入熔渣深度不变,从而保证了熔渣温度恒定及熔池形状不变,以便获得高质量的电渣锭。根据对现有电渣重熔炉电极升降控制原理的分析,开发了一套新的控制系统:采用PLC控制电极升降系统,利用计算机及Step7、WinCC等编程软件来实现控制要求,电渣炉电流摆动幅度控制在±150A。熔化速率摆动幅度控制在±0.5kg/min,电渣锭表面质量良好。
关键词:电渣重熔;电极;PID;冶炼电流;PLC
中图分类号:TP277 文献标识码:B 文章编号:1003-7241(2012)06-0109-04
1 引言
电渣重熔是利用电流通过熔渣时产生的电阻热作为热源进行熔炼的一种冶炼工艺,其主要目的是为了提纯金属,获取结晶组织均匀致密的钢锭。虽然目前已有控制技术比较先进的大型电渣重熔炉,但这些设备价格高、占地面积大、通常比较适合于大规模工业化生产。而目前大部分中、小型企业广泛使用的电渣重熔炉还是基于集成控制电路的结构比较简单、技术水平相对落后的设备。这些电渣炉设备陈旧,故障较多,特别是控制系统落后,控制精度(工作电流、工作电压、功率、熔速等)及稳定性较差,直接影响了电渣锭的质量和生产效率,制约了其经济效益的进一步提高。限于技术水平,很多的电渣炉控制系统依然采用继电器控制及恒功率的控制方式,由于控制精度不高,无法发挥电渣炉生产的最大效率。现在新改进的电渣炉控制系统以PLC为控制核心,大大提高了控制效果。
2 设备概况
福建某公司电渣炉车间采用国产设备,其主要技术参数如表1所示,改进后的控制系统由S7-300 PLC,Step7和WinCC 6.0等编程软件以及工控机组成。根据工艺要求其控制系统由下列电气设备组成:
● 一台单相1500KVA有载调压变压器;
● 一台15KW交流电机,用于控制横臂的快速升降,由现场工作人员手动操作控制电机启、停,正、反转;
● 一台4KW交流变频电机,用于控制横臂的慢速升降及熔炼速度,通过控制程序控制电机启、停、正、反转及调速;
● 一台2.2KW交流电机用于控制台车的行走;
● 二台2.2KW交流电机用于结晶器X-Y方向的微调;
● 一台3.7KW交流电机用于控制电极夹紧动作;
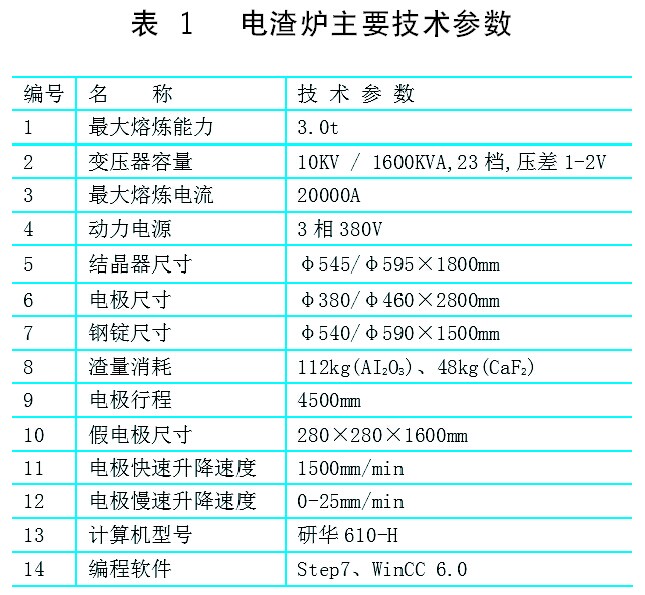
3 电渣炉冶炼工艺
电渣重熔是一种二次精炼工艺[1-2],冶炼过程如图1所示:在铜制的水冷结晶器中装有高温高碱度的熔渣,电流通过自耗电极和液态熔渣产生的电阻热使自耗电极逐渐熔化,熔融的金属汇集成滴穿过渣池进入金属熔池在水冷结晶器内强制冷却,液态金属逐渐凝固形成铸锭。电渣重熔过程中,渣池提供的反应温度高,金属在重熔的过程中与高温熔渣能充分的接触,重熔后的钢锭结晶方向近似于自下而上的轴向结晶,使重熔后的铸锭具有金属纯净、组织致密、成分均匀等优点[3]。
随着电极的不断熔化,电极与渣液的接触状态逐步减弱,为了使电极始终和渣液保持一定的接触,电极在熔化的同时应该使电极适当下降。理论上要求重熔电极下降速度与其熔化速度相匹配。下降过快会导致熔化不充分,有金属颗粒或夹渣物从电极上脱落并进入金属熔池,影响钢锭性能。下降过慢会导致电极与渣液接触状态恶化,使冶炼炉不能正常工作。
4 电极升降控制方式比较
传统的电渣炉电极升降控制系统其控制方法是通过调节操作台上的电位器给定冶炼电流,其给定电流与检测的冶炼电流比较,经PI调节器后,输出0-10V信号控制交流变频器的输出频率,从而改变慢速电机的转速。由于电极冶炼的给定电流仅靠操作人员通过电位器手动设定,通过观察检测电流及慢速电机速度的摆动幅度来决定电位器给定电流的大小,使冶炼电流摆动幅度在控制范围内。可以看出这种控制方式要求操作人员应有丰富的实践经验。同时其控制系统采用是传统的继电器逻辑控制方式,继电器控制系统接线复杂,工人的劳动强度大,故障诊断和故障排除难度大且质量不易保证。此外使用继电器逻辑控制系统还存在以下不足:
1) 传统的电气控制线路触点很容易被电弧烧损从而导致接触不良,有时还可能造成线路短路损坏设备;
2) 传统的电气控制系统其控制功能大多被固定在电气线路中,控制模式单一、灵活性差。传统的控制模式由于其控制触点多、故障率高、功能单一、可塑性差等缺点,正逐渐被淘汰。
随着计算机技术的快速发展,采用以PLC为核心的计算机控制系统成为非常适合的选择方案。PLC系统一般采用上、下位机两层结构,它不仅可以满足传统控制模式的所以功能,同时它还具有以下优点:
1) 可靠性强,不需要大量的电子元器件,控制系统维护简单,操作方便;
2) 功能性能高,抗干扰能力强,有良好的自诊断功能;
3) PLC控制系统运行稳定,抗干扰能力强;
4) 丰富的I/O接口模块。PLC针对不同的工业现场信号有相应的I/O模块与工业现场器件或设备;
5) 安装简单,维修方便。PLC硬件组态采用模块化设计,一旦某模块发生故障,用户可以通过更换故障模块的方法,使系统迅速恢复运行。
5 电极升降系统PLC控制原理
由电渣重熔的工作原理可知,若要控制冶炼电流的大小,实际上就必须控制电极下降的速度,也就是要控制带动电极下降的变频电机的转速,即控制交流变频器的输出频率。在实际工作中不同冶炼阶段电极熔化所要求的冶炼电流是不一样的,为了保证检测电流的变化与工艺要求的给定电流变化趋势相一致。变频电机的转速必须能根据给定电流的变化而变化。为了保证控制系统的高精确度,本系统以电极的冶炼电流作为控制对象。根据工艺曲线自动改变冶炼电流的给定值,根据反馈的检测电流,经PID调节模块,控制交流变频器的输出频率,调节慢速电机的转速从而达到控制电极插入熔池的深度,以实现控制冶炼电流的目的。
图2 电极升降控制系统流程图
在控制过程中必须对冶炼电流进行实时监测,为了确保正常生产时冶炼电流偏差不超过±2%,当检测电流大于给定电流超过+1.5%时,PID调节模块自动停止工作,控制系统直接将交流变频器输出频率置零,即电机转速为零,检测电流迅速降低。同时考虑到电机在运行过程中有一定的惯性,当电机下降速度归零后检测电流仍大约给定电流且电流偏差超过+2%时,控制系统将自动改变电极原有的下降的趋势,改为以恒定频率上升,从而使检测电流进一步快速回落。当电流偏差回落到+1.5%以内,PID调节模块又开始工作控制电极运动的节奏。电渣炉电极升降控制系统流程如图2所示。
6 电渣炉电极升降PLC控制系统
6.1 系统概述
电渣炉电极升降控制系统以PLC为控制核心,该系统可以快速、准确地对电渣炉生产过程中的各种工艺参数如电流、电压、冷却水温度、压力进行自动采集、实时监控。并生成历史趋势曲线。工作人员可以在主控制室实现对控制电压和控制电流的手动调节。显示系统采用液晶显示,能显示表格,曲线和实时数据,并具有抗电磁干扰能力。
6.2 控制系统组成
改进后的电渣重熔PLC 控制系统由上位机和下位机组成。上位机采用研华610-H工业控制计算机及三星740N+液晶显示器,下位机采用可编程逻辑控制器(西门子S7-300 PLC)。以实现对生产过程监控、数据采集及报表输出。
控制系统的构成框图如图3所示。工控机与PLC的通讯是通过工业网卡CP5611实现。PLC由多种模块组成,其中主要有CPU,模拟量输入模块,模拟量输出模块,开关量输入模块,开关量输出模块等。上位机与下位机采用西门子MPI协议通讯,通过控制程序,利用输入输出及信号转换模块与交流变频器连接,实现对慢速升降变频电机的控制,上位机系统采用西门子公司WinCC组态软件开发,设计组态画面。PLC系统采用西门子公司Step7软件进行编程[4]。
6.3 S7-300 PLC编程设计
西门子Step7是用于SIMATIC S7-300/400站创建、编写逻辑控制程序的标准软件,可使用梯形图逻辑、功能块图和语句表进行编程操作。用文件块的形式管理编写的程序及程序运行所需的数据。如表2所示:
表2 用户程序中主要功能块介绍[5]
6.4 WinCC组态
根据电渣炉生产的工艺要求,WinCC组态由主画面、电渣重熔运行综合工艺参数画面、电流(电压)跟踪画面、故障报警与查询画面等组成。
(1) 主画面
启动WinCC后首先进行的是主画面,它上面设置了电渣炉电极升降控制系统的简易工艺流程图和用户登入窗口,防止误操作。同时在主画面上还设置了当前的时间和日期显示。
(2) 电渣炉综合工艺参数画面
电渣重熔综合参数画面主要设置了PLC电流自动控制系统、电压控制系统、电渣炉控制方式、电极工作状态、主要设备运行参数以及各设备循环冷却水压力、温度显示。
图4 电渣重熔WinCC监控系统
(3) 历史趋势画面
主要是对电渣炉整个生产过程中电流、电压、钢锭生成速率等数据实时采集、记录与存储,生成历史趋势曲线画面。
(4) 故障报警画面
在电渣炉生产过程中,当发生过流、过压、重瓦斯、油温高、结晶器水压低及变频器运行故障等报警信号时,可以进入故障报警与查询画面来查询故障发生的时间、位置及故障处理的方法。
(5) 参数设定
在参数设定画面中,可以对生产各个阶段的控制参数进行设定,包括化渣期、重熔期、充填期的设定电流和电压等参数,同时可以设定功率递减的方式和幅度。这些数据存储在数据库中,当电渣炉需要改换熔炼工艺的时候,只需调出相应的工艺参数即可。
7 结束语
改进后的电渣重熔控制系统投产运行后,钢锭不但保持了外表面光滑,渣皮薄而均匀的特性。使用新系统后冶炼电流摆动幅度控制在±150A。熔化速率摆动幅度控制在±0.5kg/min。说明新控制系统硬件设计合理,控制精度高,软件功能完善,操作维护方便,运行可靠,并且抗干扰能力也明显提高,保证了电渣重熔炉生产运行和操作维护的需要。
参考文献:
[1] 李正邦.电渣重熔译文集[M].北京:冶金工业出版社,1990:126-127.
[2] 李正邦,邹文正,谢继莹等.电渣熔铸[M].北京:国防工业出版社,1981:1-3.
[3] 钱月平等.Ni基合金电渣重熔铸锭中孔洞形成的原因分析[J].有色金属,2009:13-16.
[4] 深入浅出西门子WinCC V6[M].北京:北京航空航天大学出版社,2004.
[5] 廖常初.PLC编程及应用[M].北京:机械工业出版社,2002.