一、前言:
自动化控制系统的历史像一部春秋战国史,受到电子、软件、PC、网络技术的影响和冲击,形成了好多流派。特别是进入上世纪九十年代后,各流派间交溶汇合,已是你中有我,我中有你,连各大门派的掌门人都有点描述不清楚咱这一派的独门功夫是什么,与少林武当的区别在哪。
常听一些在行业中多年的朋友困惑的问,PLC、DCS、PAC、FCS、NCS倒底有什么区别?选择的标准是什么啊?未来的控制系统到底是更加专业化还是更加通用化,将来还会有上面的这些名词吗?
每当此时,各厂商的专业人士总是含糊其词的说:“啊,这个问题很复杂,不是一言两词可以描述清楚的,以前还可以,但现在是越来越说不清楚了,有空我再给您详谈。”
今天借世界仪表与自动化的宝地,在这里把这些个问题给讨论讨论,一方面抛砖引玉让更多专家来关注这个课题,另一方面也给自己一个思路整理的机会,为深圳市矩形科技未来几年的研发方向看看路。(德维森科技自动化业务已于08年初转移到深圳市矩形科技)
二、控制系统发展的历史脉络
每每想把控制系统的历史脉络给整一下就头大,因为如果要讲清楚必需一个很清晰的图和详细的文字才可以,而本人是一个很懒的人,打打字还行,如果要做一个很漂亮的图就会头痛脚软,但如果没有图又不能讲清楚,所以我还是,勉为其难画了一个图,未能做很精确还请大家见谅。
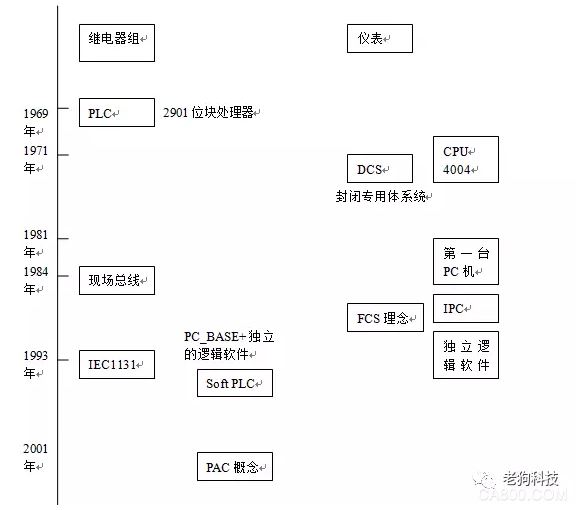
通过上图,大家可以发现,整个工业控制的历史受到了PC技术的充分影响,同时工业控制的特点又使其无法完全与PC思想完全统一。
1.PLC历史
由上图可知,早在上世纪60年代以前,主要的控制系统主要是由各种继电器组和仪表组成,其中继电器组主要用来完成逻辑和数字量控制,而仪表则主要完成模拟量回路控制。两者之间有着明显的差别。
60年代以前,汽车生产流水线的自动控制系统基本上都是由继电器控制装置构成。当时汽车的每一次改型都直接导致继电器控制装置的重新设计和安装。随着生产的发展,汽车型号更新周期愈来愈短,这样,继电器控制装置就需要经常地重新设计和安装,十分费时,费工,费料,甚至阻碍了更新周期的缩短。
为了改变这一现状,美国通用汽车公司在1969 年公开招标,要求用新的控制装置取代继电器控制装置,并提出了著名的十项招标指标,即:
1)编程方便现场可修改程序;
2)维修方便采用模块化结构;
3)可靠性高于继电器控制装置;
4)体积小于继电器控制装置;
5)数据可直接送入管理计算机;
6)成本可与继电器控制装置竞争;
7)输入可以是交流115V;
8)输出为交流115V 2A 以上能直接驱动电磁阀接触器等;
9)在扩展时原系统只要很小变更;
10)用户程序存储器容量至少能扩展到4K。
这时侯第一块8位CPU还差一年才诞生,所以DEC公司的同仁们后来采用了一种特殊的位块处理器2901,这种架构很好的满足了GE公司的要求,但这也导致了长达数十年PLC体系架构之争,现在主流的PLC仍在采用这种架构。
这个问题上很多朋友有误会,以为这么老的技术还在使用,其实不然。位块处理器其实是一个架构,这就像现在最新的PC CPU仍在使用古老的哈佛结构体系是一样的。
因为PLC最开始的定位是位逻辑的处理,如果进行过底层软硬件开发的朋友一定会明白采用一颗通用的CPU去处理位操作是多么的慢,需要把一个字中的位先通过与操作再移位,运算完后还需要通过反向的操作后再写回去,同时还需要位在字中的定位描述等。相反如果有一颗专用的处理器来处理则会变得快捷和简单很多。这种架构在处理位逻辑时相当的方便,影响深远,今天大多数的新一代高速PLC仍采用专用的位块处理器。
随着PLC技术的发展,单单的逻辑处理是远远不够的,所以现在大多数中高档的PLC都有两个CPU核,一个是通用处理器,一个是专用处理器(如矩形科技的V80和PPC11系列,其专用处理器单芯片内带梯形图专用处理器、运控处理单元、通信管理单元、IO接口、扩展总线接口等)。
当然新一代的位块处理器已远非当初的2901可以相比较,其除了完成了梯形图指令的解析和逻辑指令的运算,并通过一系列的优化,使整个系统的稳定性、可靠性、实时性都大大的提升,所以说这个位块处理器实际上已成为了中高档PLC中的核心器件,也是各大PLC厂商的核心技术。
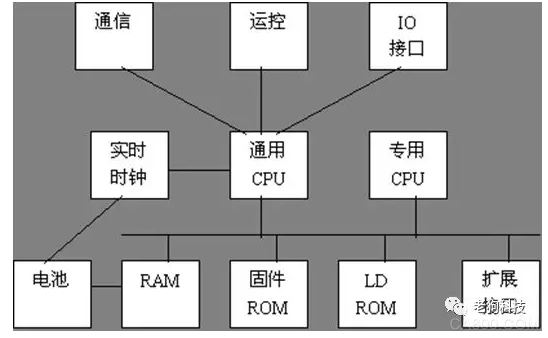
《矩形科技V80小型PLC系统结构》
简单归纳传统PLC的系统特点:程序周期循环调度机制+中断调度机制;增量式现场总线通信方式;梯形图编程方式为主;以单机运行为主;
2.DCS
自从第一台PLC诞生起,工业控制器就受到PC技术深远和重大的冲击,第一次是DCS。
分布式控制系统(DCS,Distributed Control System):其实不是一个单一的产品,而是一系列软硬件产品组合的系统,其硬件部分可以是PLC也可以是基于IPC的控制系统,早期的DCS厂商都采用封闭的软硬件平台,但很快它就受到了PC的影响,很多厂商开始采用PLC作为硬件平台,用标准的电脑加商用操作系统为操作员站、工程师站、历史服务器的软硬件平台,更有甚者采用第三方的组态软件为监控软件。特别是新一代的DCS已完全成为了一个软硬件的大集成,上面只有部分算法和优化程序是由厂商自己提供的。
《矩形公司DCS硬件系统结构图》
简单归纳大多数DCS所特有的特点可以总结为:以网络为主体架构;程序定时调度机制(10mS~NS或叫时间片调度机制);集散式的系统结构,各DPU之间通过网络互联;基于全量通信的分布式实时数据库;功能图的编程习惯;(这个归纳是不严格的,也得不到所有DCS厂商认同,但目前主流的DCS很多采用这个结构);通用或专用的操作站软件和历史服务器软件;
3.PC_BASE
1)PC_BASE的优点:
PC_BASE出现时在工控界引起了很大的反响,那个时代的控制器都是相当昂贵,而PC软硬件的低成本对于大家来说是相当大的吸引力,当时很多学者都认为PC_BASE是未来中大型工业控制系统的主流方向。当时的工程师分为两派,一派认为PC是为商用开发的,控制界只能吸收其有用的技术,而另一派认为PC技术的广泛应用,有如此之多的软件和硬件资源可供利用,对于控制器的标准化和降低成本有很大的好处。
在这个过程中,国内的工控厂商包括DCS、PLC和各种专用控制器都广泛的采用了PC_BASE结构来开发新产品,大多使用386、486、586,其中ICOP的386X_M6117D和MAPLE的486DX4-100M是其中较好的工业级X86芯片之一。(深圳矩形科技的PPC22和PPC31就是PC_BASE平台的控制系统)
2)PC_BASE控制平台的困境:(仅评论PC_BASE充当控制系统的情况,不涉及其余应用方式)
PC_BASE在近些年的发展中遇到了一些难题,当初大家之所以选用PC_BASE是因为开发方便,特别是DOS和X86兼容年代,大家可以在一周的时间编写出一个很复杂的控制类程序,在刚有网络的时候,大家通过BBS互通有无,当时感觉有一种一切均在掌握之中的感觉。
软件部分:
现在DOS使用者越来越少,于是很多厂商在引导工程师走WINNT的平台,而WINNT对于底层的屏蔽使广大底层软件开发工程师感到相当郁闷,因为WINNT体系的WDM驱动程序开发需要用到DDK等复杂工具,就算使用XTOOLS之类的简易开发工具也会让人有一种隔鞋搔痒的感觉,新一代PC硬件的复杂接口也使大家不愿意在上面花太多的工夫,让PC_BASE的开放性和方便性大大的被抵消了。同时WINNT体系的低可靠性让大多数自动化工程师望而止步。
2.0以前的WINCE也是一个让人发狂的软件,不光可靠性差,实时性也相当差劲,让人怀疑这玩意只能用来做做显示屏,后来wince2.0出来后还好一点,但个人对WINCE还是有抵触,可能是当初吃苦头吃多了,总认为一个工控产品不适合选用WINCE做操作系统,因为WINCE的系统结构包括兼容性、开放性、图形方面的优点都是针对手持消费类产品的,如PDA之类,对于工控需要的高实时性和高可靠性实在有点不及格。这一方面linux要更差一些,因为linux是为商用电脑开发的,很多公司都在为linux进行减肥并把抢占式的调度机制强行加入linux,从而可以使linux可以用在嵌入式的环境,但WINCE有的缺点它也都有,同时还要更严重,所以也不是一个好的选择。在操作系统方面,其实像VXWORKS和NECLUES之类的可能是一个不错的选择。
因为PC_BASE的这些需求,派生出了一些专业的软逻辑公司,主要是以欧美企业为主,他们为IPC厂商提供了一整套软件,使用户可以像使用PLC一样去使用IPC,从而简化了软件的开发工作。
以KW、Infortem、Isagraf为代表的软逻辑厂商结合OPEN PLC组织,大大的推动了IEC61131标准的发展,但也正因为此,其以PC_BASE为硬件平台的开发思想,导致了目前IEC61131-3部分对于软硬件资源的开销太大,大大的限制了IEC61131-3在传统领先控制器生产厂商的推广,直到目前除软逻辑厂商外的其它传统控制器厂商都只是嘴上讲支持IEC61131,而实际上与标准均相去甚远,连基本的第一级兼容都达不到。上次OPEN PLC组织的主席来国内,对于这个问题也相当坦率的承认,目前IEC61131支持的厂商还相当少,大家对于标准有很多不同的意见。
硬件部分:
对于PC_BASE体系更要命的是工业控制的软硬件发展速度远远跟不上民品的发展速度,往往民品的这一档CPU都已经停产,而工控行业才开始试用,目前低档X86的配套芯片都已停产,包括DRAM等,使大家想接着使用386、486、586都不可能了,少数正在生产的芯片也因为价格问题而很难接受。同时现在intel和微软已完全放弃了向下兼容的规则,使PC_BASE存在的意义日益减少。没有哪家工控厂商都跟上这两位大佬的更新速度,当你的产品准备面市时,你会发现你使用的所有器件均已停产,你只能上二手市场去买拆机件。
同时现在大多数主流的X86芯片是高密度封装的,包括大量的高密度的接口定义,在工业环境下的防尘、抗振、散热等问题都很难处理,前不久在航天系统就出现了加固电脑因为地震而死机的情况,从研发的角度而言这些问题都是很难解决的,因为整个体系都不是为工业设计,在586以前这一切都还可以容忍,但现在系统已经很难有办法去处理了,特别是在做成紧奏型的控制系统时这个问题更为严峻。
这也是各工控机厂商转战软PLC和PAC平台的软硬件技术来源和市场动力,通过打破PC_BASE的软硬件体系架构,再加上第三方的逻辑软件就可以实现一套很好的控制系统。
4.现场总线技术和FCS
在软PLC出现后不久后,一场全新的技术浪潮狠狠的冲击了工控行业,这就是现场总线,同时基于现场总线派生出了FCS的理念(全分布式的基于现场总线的控制系统)。
现场总线最开始只是为PLC和现场的仪表提供一个组网的功能,但很快就有人想到,如果把所有控制逻辑全分散到现场,这样就不需要把所有的电缆拉到控制室,节省了大量的成本,同时随着控制的分散后,其安全性也可以得到大大的提升,局部的故障将不再会引起整个系统的崩溃,这就是FCS的基本理论和来缘。
在8年前,我也是FCS的拥护者和实际开发者,深信在当前的通信能力、芯片能力越来越强,价格越来越低的今天FCS才是未来的控制系统,它将替代包括PLC、DCS在内的所有控制系统。可在实际的开发和应用过程中,我们发现了一些问题全分散之后不光成本升高了,维护也变得更困难,因为所有的节点都依赖网络,而网络的可靠性就变成了一个瓶颈。这么长的网线,有任何一段出现短路或者开路都会有致命的损伤。并且分散后的逻辑,会因为一个中间节点的故障导致整个系统的重大错误,当然如果用户对分布式控制理念有很深的理解当然没有问题,但事实上让用户工程师理解这么复杂的拓朴结构是不现实的。
除非未来的神经元网络芯片研发方面有新的发展(不是LON总线的3150),可以在某一个逻辑运算节点损坏后自动由另一个逻辑节点替代,同时需要更好的基于网络的逻辑编程软件,这个软件可以对于分布式的控制器进行合理的逻辑切分,并且对任一个节点损坏后出现的状况能有合理的处理方式,或是保护或是不管。FCS发展的终极理想情况是只有传感器和执行器而没有单独的控制器,所有的传感器将自己的参数传给需要的执行器,各个执行器根据网络得到的参数运算并进行控制,同时将自己运算得到的中间值传给其它的执行器。因为有了中间值的问题,所以整个控制网络将变得相当复杂,每个有中间值的点都必需有合理的处理策略,理想的情况下,是当中间逻辑点出现问题后,能由另一个逻辑点进行替代,或者进行合理的保护策略。在可以预见的时间内我们将很难开发出满足所有要求的FCS,所以我们有理由相信FCS将只会在一部分市场中得到应用。
但FCS的理念却深深的影响了PLC行业,目前大多数PLC都带有现场总线接口,实际上在FCS的争论后,PLC已具备了组成FCS的硬件需求,如矩形科技的V80系列就可以通过现场总线组成一个数千点的FCS系统。这样的后果是未来很难再存在一个独立的DAS系统市场空间,包括各类现场总线的IO模块均会由一些PLC所替代,因为其两者的成本一致,而PLC的功能还要强很多。
在经过若干年的争论和研究后,目前国内外的很多研究人员形成了一个暂时的共识,那就是:根据现场的实际情况选择分布还是集中,很多情况下一种整体分散局部集中的方式是比较适合的。比方在冶金行业,很多现场使用PPC11作为主站,用V80做为子站,把子站分布在现场,每个子站负责一个具体的控制对象或回路。这样一方面当网络出现问题时,各个子站可以很好的处理自己的任务,同时每个子站到设备的距离减至了100米以内,使布线和维护变得相对简单了。
现场总线的技术浪潮中有一个很有意思的情况,那就是IEC61158的制定,这个过程充分的反应了国际工控业各大利益集团的冲突,大家为了保护自己的利益在长达15年的时间内竟然未能达成一个真正有意义的协议,最后的结果是变成了8种标准并存,后来又扩到了13种(有14种标准,但有一种退出了),标准的范围也从最初的涵盖过程、楼宇、电力等退到了只包含过程控制。其实我个人认为做一个统一的标准包含所有行业目前来看不太现实,各个行业对成本和性能的关注点也不同,像一般过程控制大家可能选PROFIBUS等,楼控可以选LONWORKS,数采和设备间通信可以选MODBUS等。但同一行业内实在应该制定一个统一的标准,我们很多工程师都会为V80联西门子或者AB的控制系统而伤脑筋。所以不需要跟风,国内厂商间多交流多沟通多兼容,加强国产各类产品的互联性,这将是国内工控厂商以小胜大的关键,在此希望现场总线基金委员会的专家们能更务实的推动国内工控厂商在当前状况下的互通,特别是对于新研发的系统,而不要把过多的精力放在翻译国外的标准和一些纯学术的研究。
互联网对于工业控制的影响,不亚于现场总线,它的作用将在未来几年充分反映,但不会是以工业以太网的方式,而是通过网站的形式。其目的不光是提供一个通信链路,和一个人机接口,而在把装备更好的溶入我们的信息世界之中,目前比较常见的应用是包括环保监控、水文监控、路灯节能管理、公交管理、远程设备监控等,现在大家很多采用GPRS加标准的组态软件或者自行开发上位机软件,但这只是一个开始,从技术角度而言,提供一个完全开放的基于网站的组态软件平台(运行于网站之上,供众多客户自行的维护和管理),供用户自行将自己关心的设备数据取上来,并进行相关的显示、存储、处理是完全可以实现的,包括未来的智能居家、智能设备管理、设备厂商远程代维护,均可以在同一个装备网平台来完成。
我相信未来互联网最大的用户一定是不是人,而是装备,开关,每个灯泡,当网络进入装备和家居后,一个带通信的节点成本低于50元是完全可以实现的。今后最赚钱的网络不是GOOGLE之类的,而可能是现在一个名不见经传的设备网,如果能有一个一统江湖的设备网(为用户提供人与设备的接口),那才是最大的市场,设备网一定是未来工控行业最大的生意,因为它将是装备业发展的终极目标,以服务为收费手段,而不是卖产品,它隐藏了太多可供发掘的服务,将对装备行业产生核爆级的冲击。
5.PAC
PAC这个概念自从出现后在国内一直争议不断,到底什么是PAC,PAC有没有独立存在的必要?我已曾与一些同仁们争论过,多蒙这几位前辈胸襟宽广没有和我计较,后来大家还来深与我交流过。因此在争论后,我也曾思考这些问题,在这里献献丑,看能否给大家一些启发。
如前面所述,在过去,PLC、DCS、FCS、运控、IPC(仅指带软逻辑的控制器),这些控制系统的定义很清晰,各有各的传统应用领域,各有各的技术流派,但从80年代末期开始,因为受到PC和网络技术发展的影响,这种边界越来越模糊,现在连行业的专业人士都说不清道不白的地步。
从市场角度而言,客户仍跟据自己的行业习惯选用对应厂商的PLC或DCS或IPC等,但从研发角度而言,这些控制系统在技术平台上已大同小异,只存在一些细节差异。为此行业内的厂商也都很苦恼,我常见到一些PLC厂商在向传统的DCS行业进军时受到了行业习惯的阻力,需要花很多时间去解释:“其实咱们这PLC+组态软件已完全可以满足您的控制需求了,PLC现在不光可以执行逻辑,同时对于回路控制也很强,其实PLC与DCS在硬件和底层软件上是没有区别的”。
讲不清,这是很尴尬的问题。PLC、DCS、IPC、FCS在多年的发展后,已不再是原来的东西了,它们之间已经没有很清晰的区别,事实上这些控制系统已相互渗透。但是这却很难让客户接受这种观念,为此,从90年代开始各大厂商在开发自己的新一代的控制系统时,开始有心或者无心的提出一些新的名词来代替原来的控制系统,一部分厂商甚至开发了集DCS、PLC、IPC、运控于一体的新一代的通用控制平台,例如东芝等公司的综合控制系统。
为此,大家都认为没必要再传统功能划分通用控制系统,而只需要按运算能力和点数大小来区别,所以急需一个新的定义来明确这类控制系统的名称。为了争夺对下一代通用控制平台的命名权,各大厂商之间开始了一场角逐,ECS、NCS、PAC、NLC、ALC等,很多新名词接踵而来。因为不存在很清晰的质变过程,所以这一问题一直很混乱,好多新名词没有得到客户的认同,而含糊下去了。而PAC国内因为NI、GE和各大IPC厂商的宣传攻势,所以得到了很多的关注。
PAC是2001年由ARC咨询集团的高级研究员Craig Resnick提出的,因为不是特别清晰,所以各厂商纷纷根据自已的需要定义PAC,所以大家可以在网上看到很多个版本的定义,这大多是各厂商根据自已产品的特点,对其进行修改的。
我从工控网上拷得定义如下:
1)多域功能(逻辑、运动、驱动和过程)——这个概念支持多种I/O类型。逻辑、运动和其他功能的集成是不断增长的复杂控制方法的要求
2)单一的多学科开发平台——单一的开发环境必须能支持各种I/O和控制方案
3)用于设计贯穿多个机器或处理单元的应用程序的软件工具——这个软件工具必须能适应分布式操作
4)具有开放的、模块化的体系结构,适用于从工厂自动化到流程工业的单元操作
5)开放式、模块化体系结构——设计和技术标准与规范必须是在实现中开放的、模块化的和可结合的
从上文可以看出,PAC的定义很含糊,基本上现在市面上的PLC、DCS、IPC控制系统或多或少都可以满足几项,甚至很多产品支持的内容还超过上面的定义。因此PAC更多的是对于当今新一代控制系统的一个归纳,更多的是对新一代PLC功能的归纳,而不是一个新创的产品,同时PAC也为各控制系统厂商指明了一个发展的方向。
因此如果是使用者,那么就无需关心这些名词了,更多的是看这个系统是否能为您提供最好的性价比。而相反,如果是系统集成商,或者是工程人员,则可以根据客户爱好,采用不同的名词来描述您的产品。
这样讲可能会让一些PAC的支持者不满意,但这确实是我的认识,因为90年代就出现了完全满足上面要求的产品,只是当时大家更多的把这类产品称之为基于X86平台的软PLC,如深圳市矩形科技的PPC31系列,就是采用X86实时多任务平台的,支持包括IEC61131-3五种语言、JAVE、C++、内带WEB服务器,支持基于WEB的远程HMI,具有发送和接收E-Mail功能来自动传送生产和维修数据,支持复杂的运动控制功能,支持电子硬盘、以太网、现场总线等各类开放的接口,从任何一个角度其均满足于PAC的定义,但我们仍将其称之为PLC。
三、控制系统的发展方向
目前中国的大多数工控厂商都不是技术的原创者,大家只能跟踪那些世界巨头的发展方向,这是一个发展中国家不可避免的发展方式。其好处是显而易见,但也会因此而出现跟风过紧而产生的过热情况,如当年的FCS热潮,我也头脑发热的过分迷信“正宗”,从而导致在产品研发中途才发现不能适用原来所期望的所有需求,这在上世纪90年代到2004年前后不是一家两家出现这种方向的失误,后来这类产品很多成为了鸡肋,在市场上的影响也很小。
新一代的控制系统,到底何去何从,大家如何界定自己下一代产品的功能和价格,我作为一名长期从事控制系统研发的工程师在这里把自己的想法和大家交流一下,因为只是一家之言,必定会有些片面和狭隘,还请各位专家多多指正。
在前一章,我们花了很多篇幅来讲各种控制系统的来龙去脉,并且认为现在再按传统的方式划会控制系统已不合适,所以才有了PAC之类的概念。那未来的控制系统从应用的角度而言应如何划分呢?为了简化说明,我们仍是以PLC为中心来讲解,避免范围太宽。
1.从市场角度
未来的通用控制平台,首先根据应用类型来划分,我们习惯于把控制系统分为三大类:
1)工程项目型——工程自动化项目,如冶金、造纸、电力、石化等
2)OEM型——批量生产的装备自动化控制,如电梯、纺织、包装、水处理等
3)定制专用型——当OEM单一厂商单一品种的稳定性比较大,年销售量超过一定数量,如1000台,则采用定制开发的专用控制系统会是一个更加好的选择,如注塑机、空压机等。
对于第三类,因为不是属于通用控制系统的范畴,所以我们不多讲,重点放在工程项目项和OEM型上面。
工程项目通用控制系统,一般点数相对较多,同时经常会与组态软件、数据库、ERP之类的软件同时使用,在此体系中组态软件的功能除了作为了一个人机接口外,还将在控制系统与第三方软件接口时起到一个万能接口的作用,如与ERP、数据库等,传统上一些大型的DCS都自带组态软件,技术方面的原因是第三方的组态软件无法在大数据量吞吐方面满足系统的要求,但随着各软件公司技术的完善,这将不是一个大问题,已有很多公司比较好的处理了些类问题。
工程项目需要的控制系统通常会希望有更开放的接口和更强大的功能:
1)更开放的软件开发环境,可以根据不同的项目选用不同的开发环境,某些优化算法,还可以采用标准的高级语言来完成。
2)更开放的硬件开发环境,在同一CPU平台或多CPU在一个系统内数据共享,支持包括PLC、IPC、DCS、FCS、运控等各种功能。
3)支持多种通信协议,可将各类现场总线接入系统,从而使第三方的产品更容易的集成进系统。
4)更强大的智能调试工具,包括各类闭环控制、PID、通信、运控、数据趋势等,减少对于工程人员经验的依赖性,提供更多的辅助工具来协助调试。
OEM型的通用控制系统,一般点数比较少,256点就可以满足大多数的装备控制了,大多数都是中小型PLC为主,装备控制系统,表面上看点数少,但实际上其技术复杂度经常相当的高,同一套设备内运控、温控、通信、人机常常同时出现。因为很多装备都是批量生产的,需要有较好的性价比,因此OEM型通用控制系统通常需要如下功能:
1)以图形化编程为主的开发环境,目前在OEM应用中还看不出有能代替梯形图的语言;
2)控制器CPU模块的集成度越来越高,相当多的功能集成进来,包括运控、温控、通信等功能,特别是运控功能,将会在PLC平台上大放异彩,将CAD文件通过编程软件处理成运控指令后在PLC平台上运行是一个必然的过程,目前在技术上并不存在瓶颈,需要的是有厂家先一步去完善;
3)通信能力越来越强,与变频器,仪表间的模拟量接口,现在已越来越多的被通信方式替代,同时控制器间的组网功能越来越强,随着国产PLC的兴起,其价格也越来越低,必将会大大的冲击传统DAS行业,很多做数据采集模块的厂商都将会受到带通信接口的PLC的影响;
4)更低成本,目前小型PLC市场两极分化严重,一方面很多设备需要更高性能更多功能的小型PLC,另一方面很多用户需要更便宜的价格,目前已有32点100元左右的国产PLC出现,在这种成本压力下,很难保证个条件都满足,所以现在各厂商大多提供多个系列的小型PLC供选择,如深圳市矩形科技的V80就是高端的小型PLC,功能强大,指令丰富,而V60则是低成本的微型PLC。
2.从技术角度
从技术角度而言,传统通用控制系统应从软件和硬件两个角度来看。
通用控制系统有几种主流的架构:
1)通用CPU+解释方式执行;以DCS和部分小型PLC、软PLC、PAC为代表,这种方式的缺点是速度相当慢。
2)通用CPU+编译方式执行;部分小型PLC、软PLC、PAC是这种技术方式如矩形科技的V60,这种方式的速度比解释方式的快20倍以上,缺点是生成代码的不可预测性和下位机程序无法上传的缺点,使其安全性有先天的问题。
3)通用CPU+专用处理器;中高档的PLC采用此类技术方式的比较多,如AB SLC500、ControlLogix、施耐德Quantum、西门子300、400、三菱Q系列、矩形科技的V80、PPC11等均采用此结构。这种方式的原理性可靠性和速度是最快的,比编译方式快20倍以上,并可以很容易的提升,缺点是成本相对于前两种要高。正因为其安全性,所以目前我们的军品系列就是采用这种架构,在众多的炮、车、舰、弹上得到了充分的考验,同时现在正在此平台上开发航天专用的控制平台。
4)SOC专用芯片,将通用CPU、专用处理器、周边功能均集成在同一个芯片内,这在新一代的PLC中有不少的应用,其性价比均相对较高,如矩形科技正在研发的N80系列。这种方式的性能与方式3一致,批量成本要大大低于方式3,但开发成本和开发难度相对较高。
具体哪一种技术比较好,比较先进,只能说根据不同的应用领域选择最合适的技术。在90年代时因为电子技术发展速度相当快,CPU的速度对于工业控制要求而言是足足有余的,所以当时兴起了一阵软PLC和PC_BASE的技术热潮,当时大家均认为这将是未来的发展方向,但令人感到诧异的是电子技术发展过快,使为民用设计的PC_BASE技术对于工业应用已有点不太适应(主要是器件的更新换代和几个体系结构,这种情况正在加剧)。所以软PLC技术脱离了PC_BASE平台而更多的采用MCU平台,如ARM等。同时目前的瓶颈不在速度,而在于通信、运控等功能,这些功能采用软件方式很难做强,所以一般现在的中高档软PLC均会通过增加FPGA来提升这一块的性能。
另一方面,主流厂商采用专用的处理器来提升系统稳定性和整体性能,同时受新一代电子开发思想,更多的可编程逻辑器件如FPGA和半定制芯片的成本越来越低,软件与硬件的边界正越来越模糊,更多的硬件开发工程师在使用硬件描述语言如VHDL或者Verilog语言开发出更专业更适合工业控制使用的专用处理芯片,这种体系架构的稳定性、可靠性、功能的强大都不是软PLC可以比拟的,同时还可以将PLC上必不可少的周边功能通过硬件来实现,如运控功能、通信协议底层高速处理、IO接口、扩展接口、存储单元的安全性管理和维护等等。如矩形科技的V80就采用了这一体系架构,从而使其在系统的稳定性、可靠性、易用性上有着很多先天的优势。
软PLC在过程控制和低成本的微型PLC方面将有着很好的发展,大量100元左右的国产PLC将在这一两年中涌现,大多都会采用这种体系架构,并将因为成本的大大下降而进入民品和居家生活之中,市场并不会因为单价的下掉而受影响,相反很多以前用不起PLC的行业将因为成本可以接受而纷纷改用PLC。
而硬PLC将会在FPGA、SOC技术的普及下会越来越显眼,特别是在OEM行业,这个优势正越来越明显,大量的运控、通信的应用需要更稳定、更确定的响应,同时其在中大型的控制系统中,也会因为硬件技术可以使系统架构更清晰和稳定,而广泛使用。我认为在软硬件边界越来越模糊的今天,这类技术方向是相当适合工控要求的。同时各主流厂商均是自行开发其专用的专用处理器,国内厂商需要花费更多的精力才有可能追上国外的领先企业。
另外一种颠覆性的体系架构正在酝酿中,未来现场工程师开发的代码将不光在CPU这一层运行,很多需要高速和高可靠性的代码将直接生成RTL文件供FPGA运行(软硬件混合开发),这将使PLC具备nS级的响应速度,一部分高要求的逻辑将由硬件直接处理,这将会使PLC具有更强大的性能和更高的可靠性,很多原来需要外部器件的现在均可以在PLC内实现,如三相的相序检测和保护就完全在PLC内实现了,包括很多保护器都完全可以在PLC内实现,其时延可以是nS级的设置,从而使PLC的市场会越来越大。
3.工控电子
传统上工控电子的发展是以民用电子为参照物的,在过去工控电子大约落后民用电子5年左右,现在这个差距已越来越大了,甚至于工控电子在某些技术方面正在脱离民用电子的架构,自成一派,不再跟着民品走。
IC的工艺尺寸越来越小,0.18um成为了标准工艺,导致IC的内核电压越来越低,这使工控现场基本无法使用,我们曾经测试过很多种新一代的IC器件,其内核电压大多是1.2、1.8、2.5V在受到同样强度的电磁干扰时,很多器件不是复位就是直接损坏,这需要广大的工控厂商引起足够多的注意,否则很有可能导致产品的可靠性低寿命断。
四、结束语
未来不是一种技术可以包打天下,各种技术将相互交溶,今天的所有视角均是站在过去技术基础上展望的,未来的方向是一大批有开创能力的厂商和工程师开拓出来的。中国工业控制系统,在经过80年代和90年代的停顿和低谷后,终于迎来了发展的高峰,众多优秀的工程师投入了这一波的发展浪潮,更难得很多厂商没有简单的破解或者照搬国外的同类产品,而是根据国内的特点开发出有自己特色的产品,我们有理由相信在未来的几年内,国产的工控厂商不光会占领国内市场,而且还会走出国门成长成世界级的工控巨头。
强大的工控产品研发能力是一个国家军事、工业现代化的基础,没有强大的控制系统就没有强大的装备制造业,没有强大的装备制造业就没有强大的生产加工能力。
工业控制系统乃国之重器,岂能容大权外落!